Monitoring costs is a critical aspect of successful construction project management. Staying within budget ensures projects are completed on time and meet financial expectations. As costs fluctuate throughout a project’s lifecycle, understanding and predicting these changes is key to maintaining control. This is where “cost forecasting” comes in. Cost forecasting is a process used by project managers to estimate future costs, helping to identify potential financial risks and avoid budget overruns.
What Is Cost Forecasting?
Cost forecasting in project management refers to the process of predicting future project costs based on current progress, historical data and performance trends. It involves estimating the remaining costs needed to complete a project. Project managers use cost forecasting to track how well the project is staying within its budget, anticipate future cost overruns, and make adjustments to keep the project financially on track.
Cost forecasting can be done on Gantt charts by linking tasks to estimated costs, durations and assigned resources, allowing project managers to visualize how expenses accumulate over time and adjust as needed.
ProjectManager has robust Gantt charts that are effective for cost forecasting because they integrate task scheduling with real-time budget tracking and resource allocation. As tasks are updated—whether progressed, delayed or reassigned—our software automatically recalculates cost projections, giving teams up-to-date financial insights directly from the timeline.
This live connection between schedule and cost helps forecast budget outcomes more accurately, control spending and make proactive decisions to keep construction projects financially on track. Get started with ProjectManager today for free.
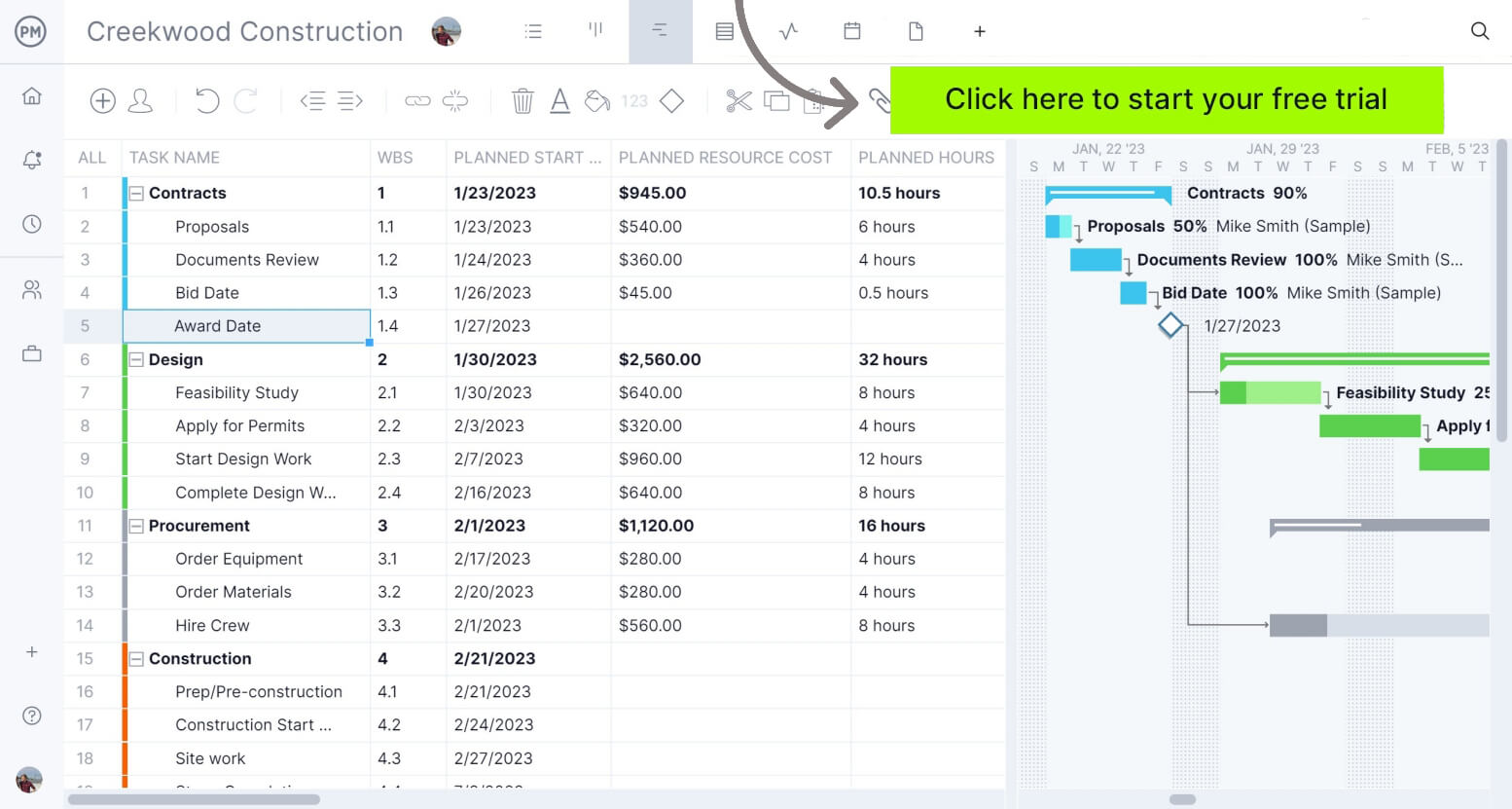
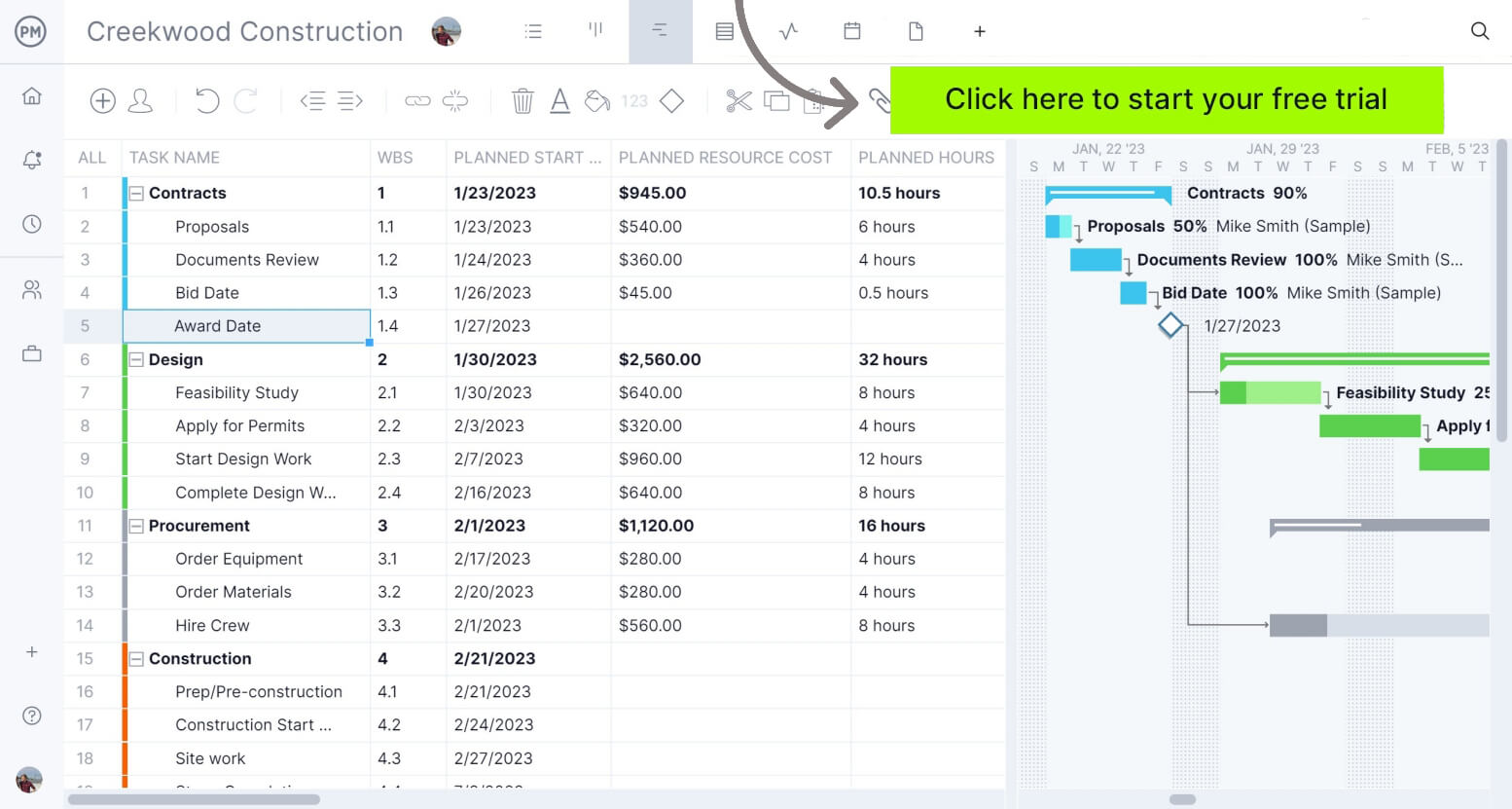
Why Is Cost Forecasting Important for Managing Construction Projects?
Cost forecasting is essential in project management because it allows teams to estimate how much a project will cost at completion. It helps identify potential cost overruns early, enabling corrective actions to be taken before it’s too late. Accurate forecasting improves financial planning, supports informed decision-making and boosts stakeholder confidence by keeping expectations aligned with reality throughout the project lifecycle.
In construction, cost forecasting helps manage risks like material price changes, labor shortages and scope changes. It ensures resources are allocated wisely, preventing unexpected overruns that could derail project schedules and profitability.
When Should Cost Forecasting Be Done in a Construction Project?
Cost forecasting should begin immediately after the project budget is finalized and continue consistently throughout the execution phase. It’s a dynamic process that requires frequent updates—typically monthly or at key milestones—to reflect actual costs, work progress and potential risks.
Forecasting helps detect budget deviations early so corrective actions can be taken. Waiting too long can lead to inaccurate predictions, while forecasting too soon may lack real data. In construction projects, where delays and cost changes are common, regular forecasting ensures better control, more accurate cash flow planning, and stronger alignment between budget expectations and project realities.
Related: 18 Best Construction Scheduling Software of 2025
The Cost Forecasting Process
The cost forecasting process consists of several key steps that help project managers predict future expenses and manage budgets effectively. Each step builds on the previous one, creating a structured approach to monitoring project financials. By following this process, construction teams can anticipate overruns, control spending, and deliver projects that meet budget expectations.
In this section, we’ll explain how to forecast costs for an ongoing construction project with earned value management formulas and then we’ll illustrate the process further with a cost forecasting example so you can better understand how to use these calculations to forecast the costs of a construction project.
1. Establish a Project Cost Baseline
The first step in cost forecasting is to establish a project cost baseline. A project cost baseline is the original, approved budget for the entire project. It includes all estimated costs for labor, materials, equipment, and subcontractors, along with any allowances or contingencies. This baseline serves as the foundation for tracking and comparing actual costs throughout the life of the project.
Establishing a cost baseline is crucial because it gives the project team a clear financial benchmark. Without it, there’s no reliable way to determine whether the project is over or under budget. The baseline enables comparisons with actual costs and progress, allowing for early detection of cost variances and more accurate forecasting as the project unfolds.
2. Identify the Budget at Completion (BAC)
With your cost baseline in place, the next step is to identify the budget at completion (BAC). The budget at completion (BAC) represents the total cost of the project as originally planned. It’s the sum of all allocated budget values for each component of the project and reflects the full financial scope of work. BAC is a static figure that doesn’t change unless the project scope is formally revised.
Calculating the BAC is essential to the cost forecasting process because it provides the reference point against which actual costs and earned value are measured. Without knowing the total budgeted cost, project managers can’t evaluate performance or predict the total cost at completion. BAC also enables key forecasting metrics like estimate to complete (ETC) and estimate at completion (EAC).
The formula to calculate the budget at completion is:
BAC = Sum of all cost accounts in the baseline
3. Make a Cost Breakdown Structure (CBS)
Once the BAC is identified, break that figure down using a cost breakdown structure (CBS). A cost breakdown structure (CBS) is a hierarchical representation of all project costs, organized by work packages or cost categories. It aligns with the work breakdown structure (WBS) and assigns budget values to each component, making it easier to monitor costs at different project levels throughout the construction process.
A CBS is essential to the cost forecasting process because it provides structure and clarity. It breaks down the total budget into manageable sections, allowing for precise tracking of expenditures. With a CBS in place, project managers can pinpoint where overruns are occurring and update forecasts more accurately. It also supports transparency and consistency when reporting project financials.
4. Assess Cost Variance
After cost tracking is in progress through the CBS, the next step is to assess cost variance. Cost Variance (CV) is the difference between the earned value (EV) of work performed and the actual cost (AC) incurred. So, cost variance is calculated as CV = EV − AC. A negative CV indicates the project is over budget, while a positive CV means the project is under budget at that point.
Assessing cost variance is vital for understanding how project costs are tracking against the plan. It provides real-time feedback on financial performance, enabling early intervention when issues arise. Without monitoring cost variance, small deviations can grow unnoticed. In cost forecasting, CV helps identify patterns and trends, which inform more accurate projections of future spending and overall budget outcomes.
So, the formulas to calculate cost variance are as follows:
- AC (Actual Cost): The total cost incurred for the work completed to date.
- EV (Earned Value): EV = % of Work Complete × BAC
- Cost Variance (CV): CV = EV − AC
5. Calculate the Cost Performance Index of the Project
After assessing cost variance, the next step is to calculate the cost performance index (CPI). The cost performance index is a key performance metric that measures cost efficiency on a project. It is calculated as CPI = Earned Value (EV) ÷ Actual Cost (AC). A CPI greater than 1 indicates cost efficiency, while a value less than 1 indicates inefficiency.
CPI is crucial in cost forecasting because it reflects how effectively the project is using its budget. A consistently low CPI signals cost overruns, while a stable or improving CPI builds confidence in your financial planning. It also feeds directly into forecasting formulas like estimate at completion (EAC), helping you predict the total project cost based on real-time performance trends.
Related: 20 Free Excel Construction Templates
6. Analyze Remaining Scope
With performance metrics in place, it’s time to analyze the remaining scope of work. This step ensures that forecasts aren’t based solely on past performance, but also on what’s still ahead. Factors like weather risks, labor availability and material lead times can affect the cost to complete remaining tasks. Understanding the scope left to execute allows for a more informed and realistic forecast that reflects both current progress and upcoming challenges.
7. Forecast the Estimate to Complete (ETC)
Once the remaining scope is understood, the next step is to forecast the estimate to complete (ETC). Estimate to complete is the projected cost required to finish all remaining project work. It can be calculated using actual performance data or by manually re-estimating the unfinished tasks based on current conditions and resource needs.
ETC is essential to the cost forecasting process because it tells project managers how much more funding will be needed. Whether calculated using historical trends or updated productivity assumptions, ETC helps refine cost expectations and adjust spending plans. It’s especially useful in construction projects, where field conditions and resource availability can shift rapidly, impacting how much it will cost to complete the job.
The formula to calculate ETC (Estimate to Complete) is:
ETC = (BAC − EV) ÷ CPI
8. Calculate the Estimate at Completion (EAC)
With ETC in hand, the final step is to calculate the Estimate at Completion (EAC). Estimate at Completion is the total projected cost of the project at its conclusion. It combines actual costs incurred with the forecasted cost to complete. One common formula is EAC = Actual Cost (AC) + Estimate to Complete (ETC).
EAC matters because it gives a full view of the project’s expected financial outcome. It allows project managers to communicate with stakeholders about total budget expectations and flag potential overruns before they happen. EAC is also a key benchmark for decision-making, helping determine whether the current plan remains viable or needs financial realignment.
There are three formulas to calculate estimate at completion (EAC), each of which can be used for specific cost forecasting purposes:
Formula 1: EAC = AC + ETC
- Use when: You have manually re-estimated the cost to complete the rest of the work.
- Assumption: Future work will not follow past trends, so you trust a fresh estimate for the remaining cost.
- Best for: Unique or changing conditions (e.g. new contractor, revised scope, better productivity)
Formula 2: EAC = BAC ÷ CPI
- Use when: You assume the project’s current cost performance (CPI) will continue for the rest of the job.
- Assumption: Future work will be completed with the same level of cost efficiency as the past.
- Best for: Stable, predictable projects where historical performance is reliable
Formula 3: EAC = AC + (BAC − EV)
- Use when: You believe future work will proceed as originally planned, regardless of current performance.
- Assumption: Past inefficiencies were one-offs; the rest of the job will go as planned.
Cost Forecasting Example
Let’s walk through a realistic example of cost forecasting using an ongoing commercial building renovation project. The goal is to apply each step in the cost forecasting process to track the project’s financial health and predict the final cost at completion.
1. Establish a Project Cost Baseline
The approved baseline budget for the renovation project is $500,000. This includes all expected costs for demolition, framing, electrical work, HVAC installation, interior finishes, and contingency funds.
2. Identify the Budget at Completion (BAC)
The Budget at Completion (BAC) is the total planned budget for the project:
BAC = $500,000
3. Make a Cost Breakdown Structure (CBS)
The budget is divided into major components:
- Demolition: $50,000
- Framing: $120,000
- Electrical: $80,000
- HVAC: $100,000
- Interior Finishes: $130,000
- Contingency: $20,000
4. Assess Cost Variance
Let’s say that by week 8 of the project:
- Actual Cost (AC) = $260,000
- Work Completed = 40% of the project
- Earned Value (EV) = 40% × $500,000 = $200,000
Cost Variance (CV) = EV − AC = $200,000 − $260,000 = −$60,000
The project is $60,000 over budget at this point.
5. Calculate the Cost Performance Index of the Project
A CPI of 0.77 indicates poor cost performance — the team is getting only $0.77 of value per $1.00 spent.
CPI = EV ÷ AC = $200,000 ÷ $260,000 = 0.77
6. Analyze Remaining Scope
The remaining 60% of the work includes HVAC, interior finishes, and some electrical. Market volatility and labor shortages are likely to affect the HVAC and finish costs. The team anticipates slower productivity than originally planned.
7. Forecast the Estimate to Complete (ETC)
Using the CPI-based formula:
ETC = (BAC − EV) ÷ CPI = ($500,000 − $200,000) ÷ 0.77 = $389,610
8. Calculate the Estimate at Completion (EAC)
Let’s calculate EAC using three different methods:
Formula 1: EAC = AC + ETC
This formula should be used when future costs have been re-estimated based on current trends.
EAC = $260,000 + $389,610 = $649,610
Formula 2: EAC = BAC ÷ CPI
This formula should be used when it’s assumed that current cost efficiency will continue.
EAC = $500,000 ÷ 0.77 = $649,350
Formula 3: EAC = AC + (BAC − EV)
This formula should be used when it’s assumed that future work will go according to plan despite earlier issues.
EAC = $260,000 + ($500,000 − $200,000) = $560,000
Related Free Project Cost Tracking Templates
There are more ways to do cost forecasting in construction or any project than project management software. There are free templates available, which can help, though they’re not nearly as efficient as software. Still, for those not ready to upgrade, these free templates offer a workaround.
Cost Breakdown Template
Download this free cost breakdown template to itemize all project expenses—such as labor, materials, equipment and other fees—by category, quantity, unit cost and total amount. It helps with cost forecasting by providing a clear, organized view of where money is expected to be spent, making it easier to estimate total project costs and predict potential overruns. By tracking actual costs against these detailed estimates, project managers can adjust plans early, improve financial accuracy and ensure the project stays within budget.
Cost Benefit Analysis Template
Use this free cost-benefit analysis template to compare the expected costs and benefits of a project or decision, helping determine its overall value and feasibility. It includes sections to list direct and indirect costs alongside tangible and intangible benefits. This template helps with cost forecasting by identifying all potential financial impacts up front, allowing project managers to evaluate whether projected benefits outweigh expenses. It supports smarter budgeting decisions and helps forecast long-term cost-effectiveness with greater confidence.
Project Budget Template
This free project budget template is used to estimate, allocate and track all financial resources needed for a project, organized by categories like labor, materials, equipment and other costs. It helps with cost forecasting by providing a clear financial plan that outlines expected expenses over time, enabling project managers to predict future spending, compare planned vs. actual costs and adjust budgets proactively. With this visibility, teams can better manage resources, avoid overruns, and ensure the project stays financially on track from start to finish.
ProjectManager Is Advanced Project Cost Tracking Software
Unlike static templates that require manual updates and offer limited visibility, ProjectManager is robust cost-tracking software that delivers real-time insights and automation across every phase of a project. Its live dashboards give an instant overview of budget health, helping teams spot overspending early.
Customizable reports break down costs by task, phase or resource, offering detailed analysis for smarter decision-making. Paired with secure timesheets, which track actual labor hours and feed directly into cost calculations, our software ensures that every dollar spent is accounted for, keeping projects accurate, transparent and financially on track.
Watch our brief video below for more on how our software supports construction projects.
Track Costs With Multiple Project Views
ProjectManager’s multiple project views—including Gantt charts, task lists, kanban boards, calendar views and spreadsheet-style sheets—work together to deliver powerful, flexible cost forecasting and tracking. In the Gantt chart, project managers can visualize how scheduled tasks and assigned resources drive projected costs over time, while the sheet view offers a detailed, spreadsheet-like breakdown for precise cost input and analysis.
The task list and kanban board allow teams to track progress and update time or resource usage at the task level, with real-time syncing across views. This integrated visibility ensures accurate forecasting, helps identify budget risks early and supports ongoing cost control throughout the project lifecycle.
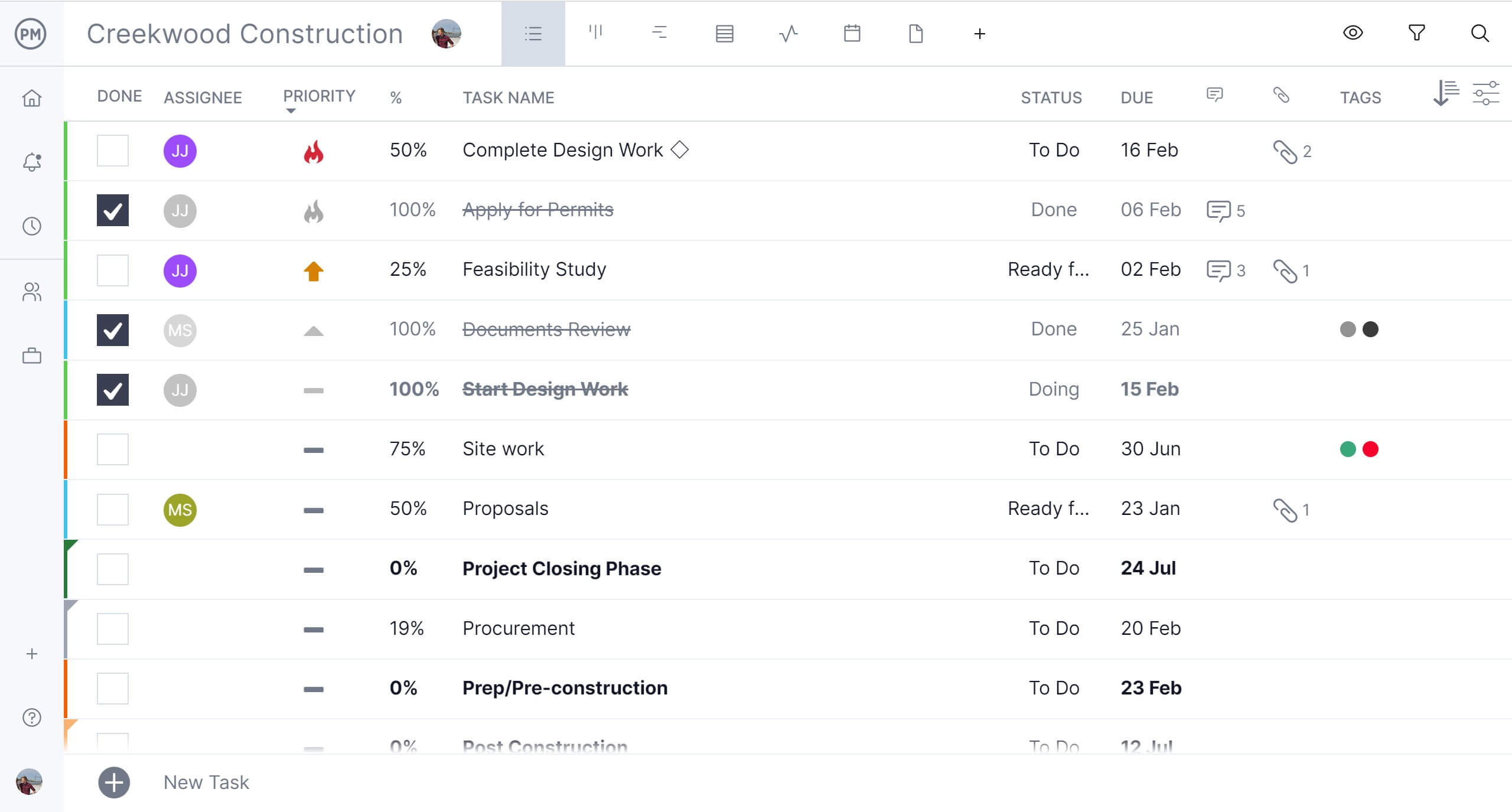
Monitor Costs With Resource Planning Features
ProjectManager’s resource planning features give teams the tools to allocate and manage labor and materials effectively, helping keep projects on schedule and within budget. The team page centralizes resource availability, skill sets and assignments, making it easy to match the right people to the right tasks.
The color-coded workload chart visually highlights overallocation or underuse, allowing managers to balance workloads across the team. With real-time availability settings, you can account for holidays, time off or part-time roles, ensuring schedules are realistic and efficient. These tools work together to optimize resource use, prevent bottlenecks and improve overall project performance.
Related Project Cost Management Content
Project cost management is a topic too large for one blog post. For readers who are interested in digging deeper into the subject, check out the links below. They cover cost control, cost estimation and much more.
ProjectManager is online project and portfolio management software that connects teams whether they’re in the office or out in the field. They can share files, comment at the task level and stay updated with email and in-app notifications. Join Teams at Avis, Nestle and Siemens who are using our software to deliver successful projects. Get started with ProjectManager today for free.